Responsibly produced jewelry.
It is my intention to use as much recycled metal that I can without compromising the integrity and strength of a piece. I purchase scrap sterling and other metals from facilities that sell the scrap from larger projects. Recycled silver is one of the best materials for the environment and the most ethical option because there's no newly mined material. I use upcycled and recycled components with respect for resources, the environment and people.
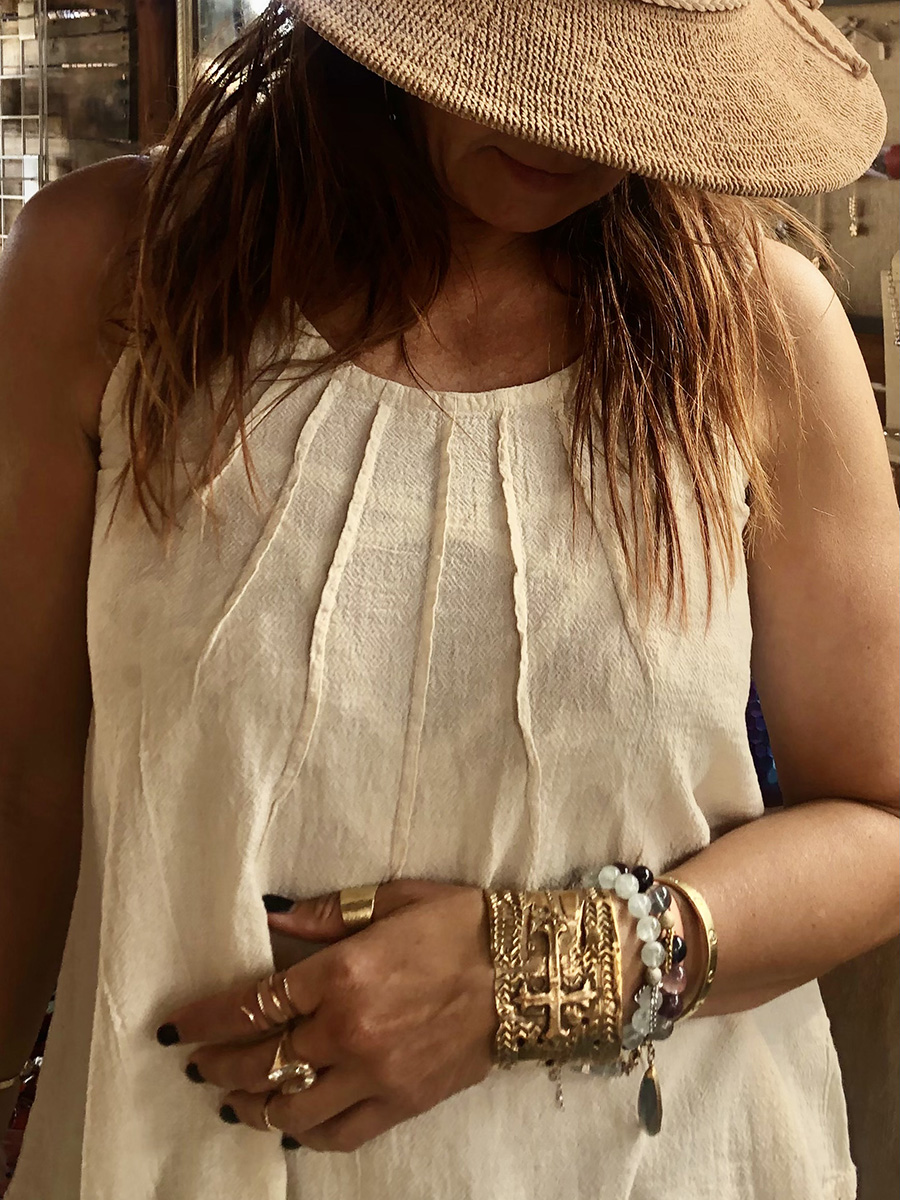
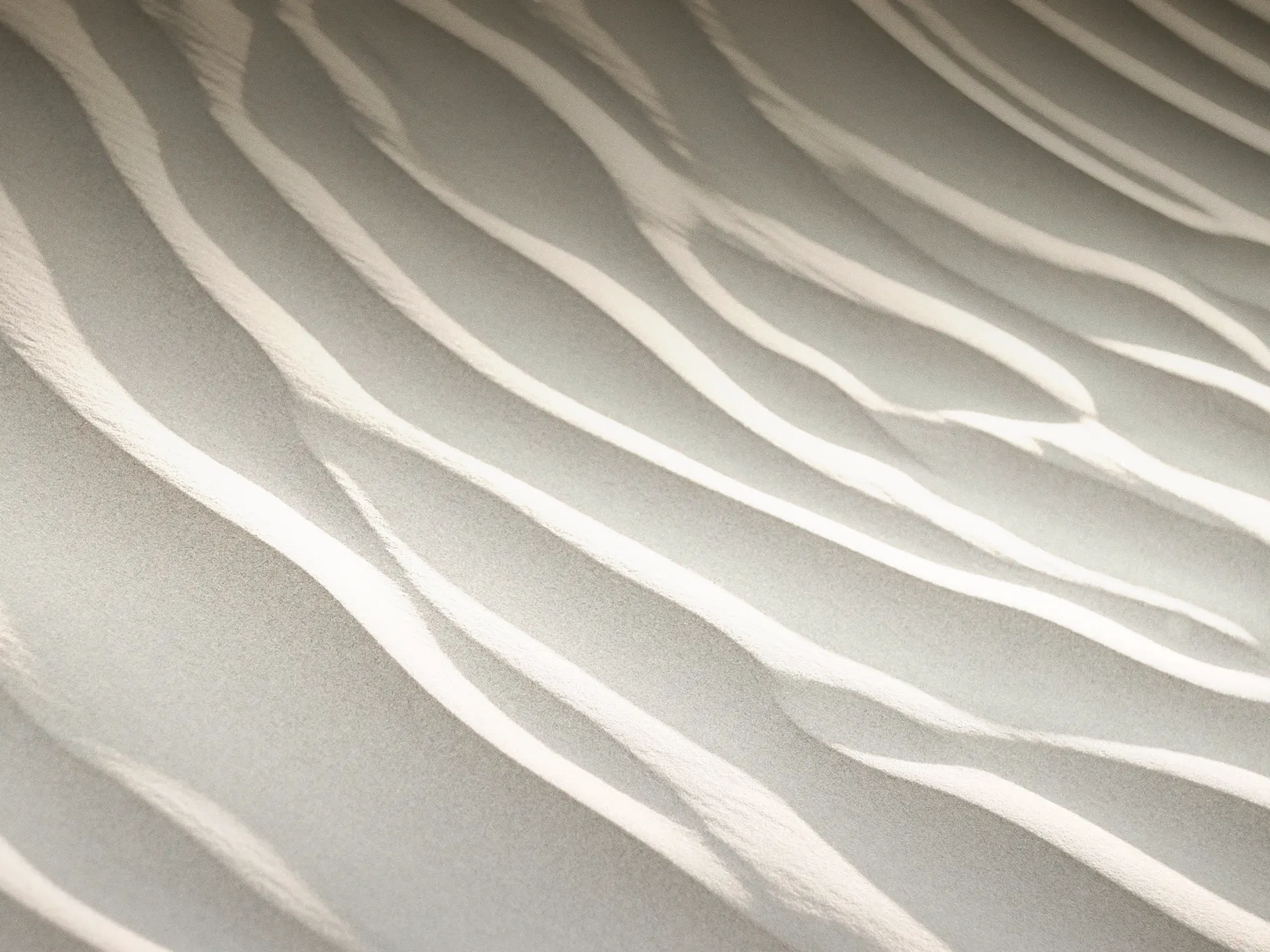
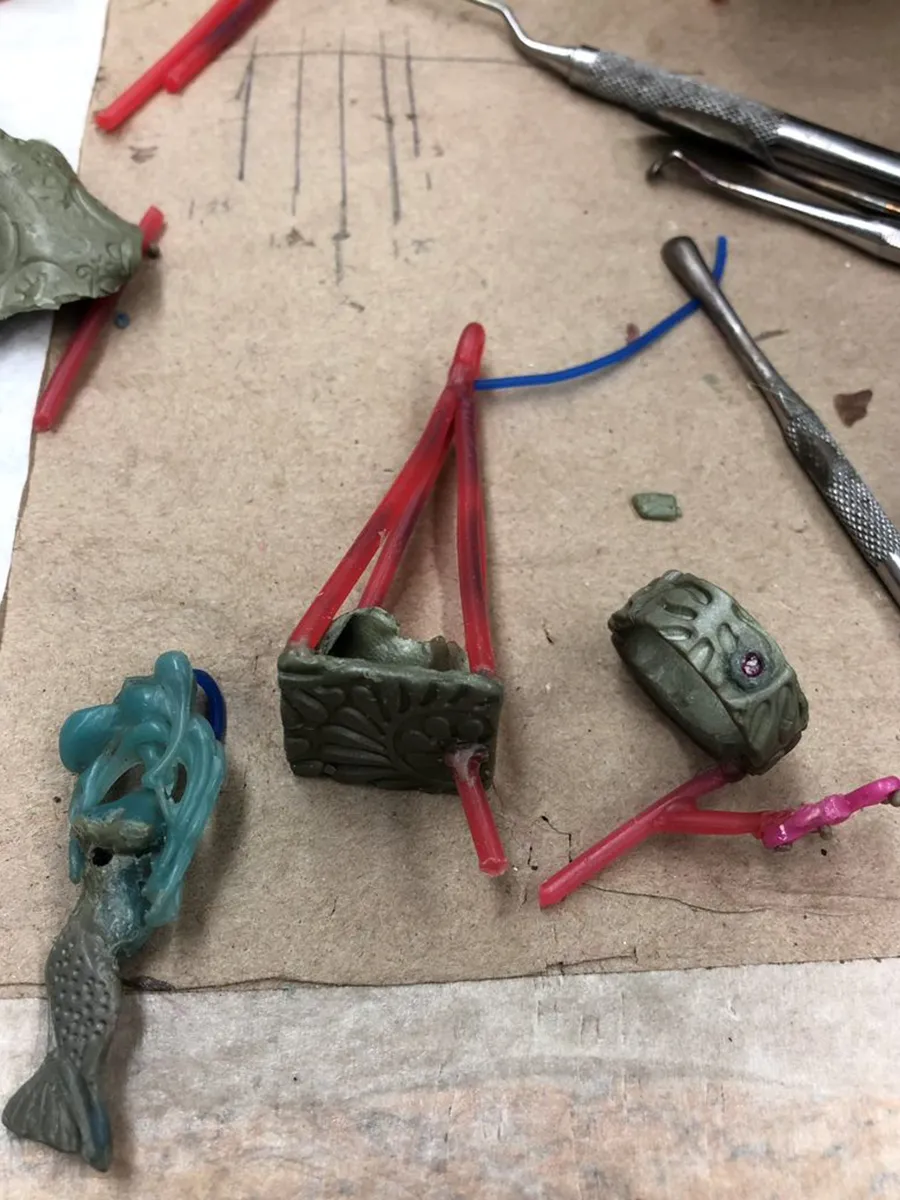
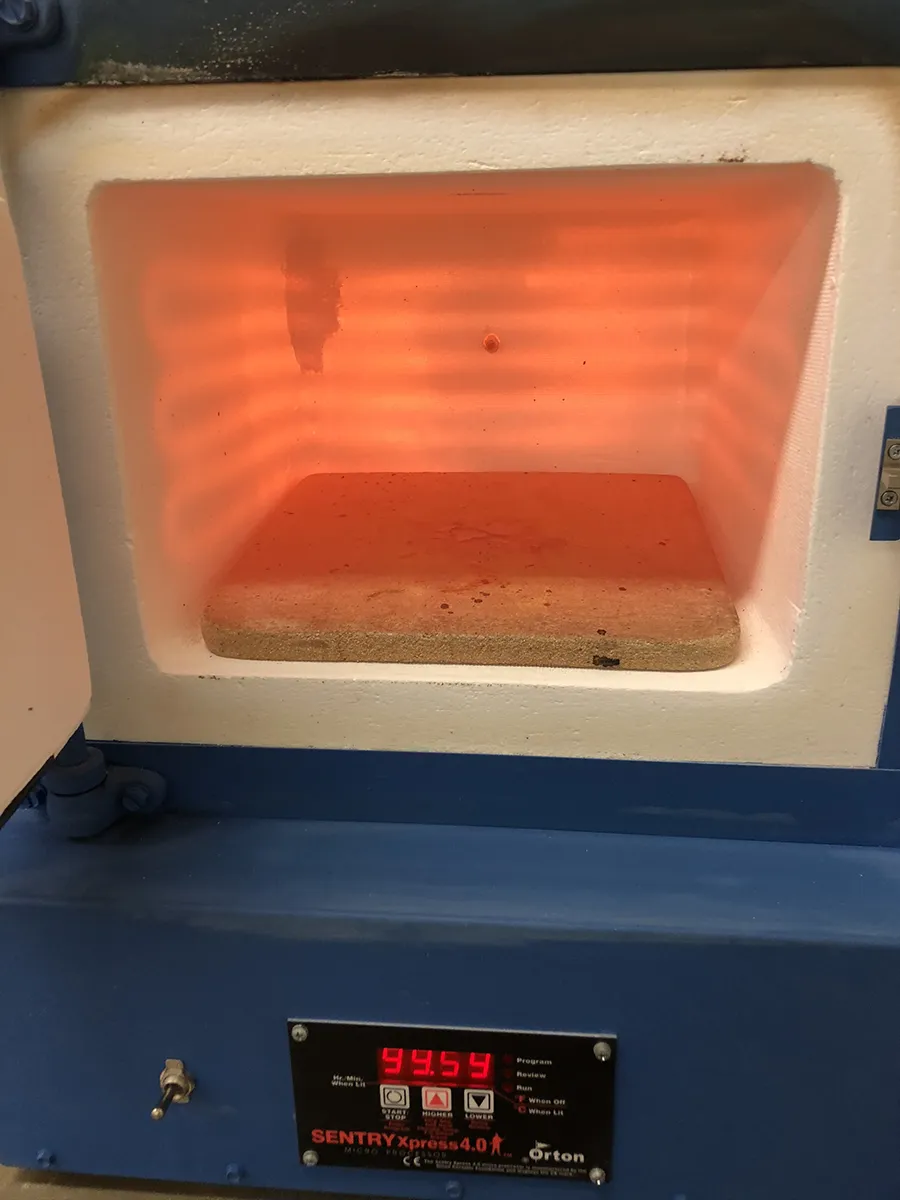
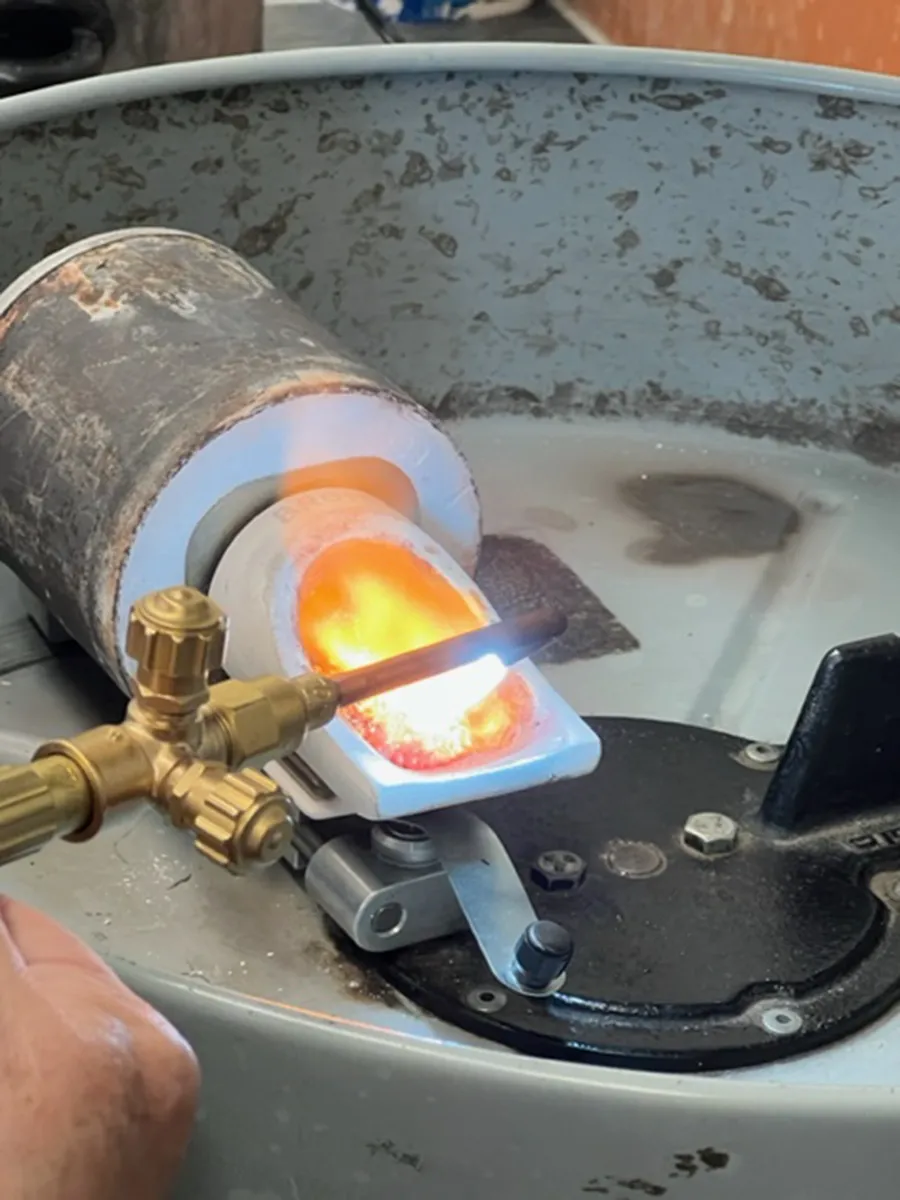
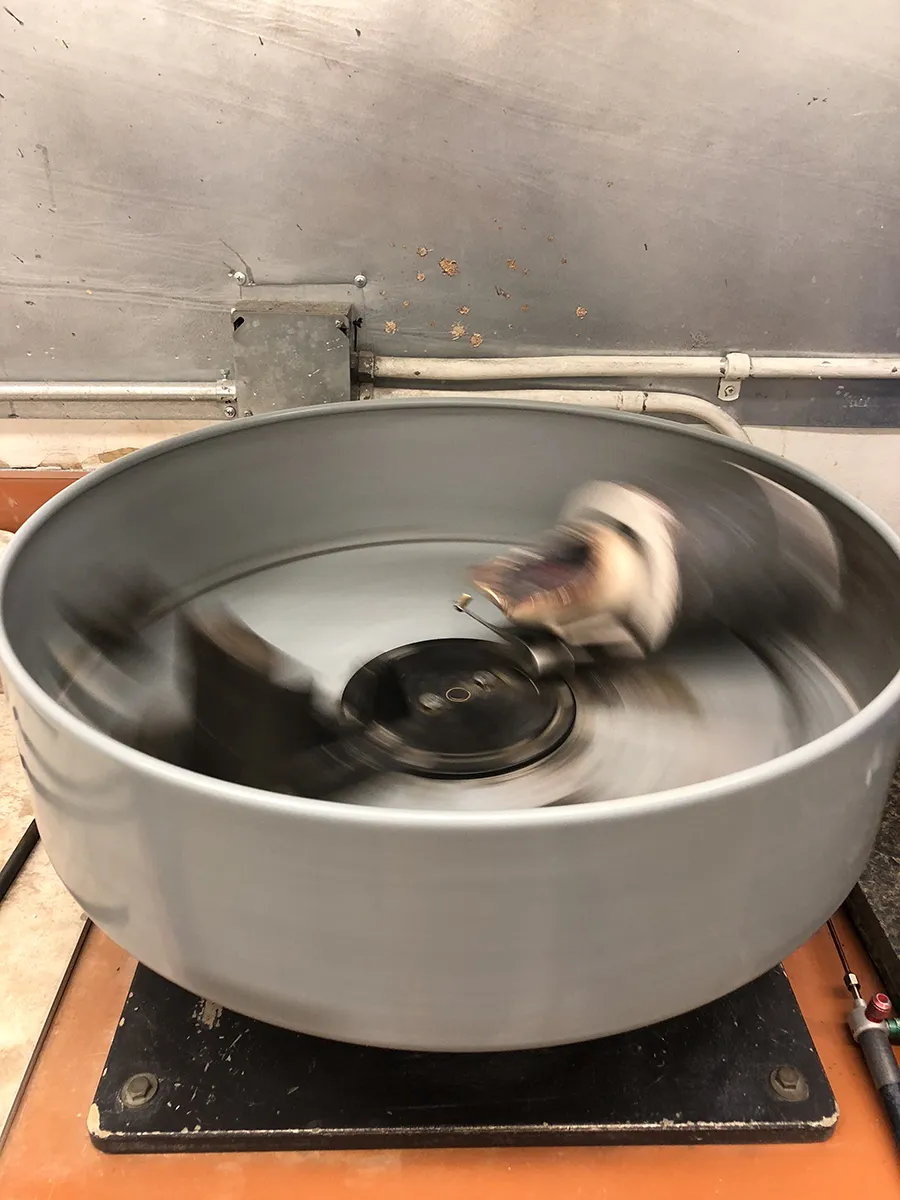
Creating and casting lost wax jewelry.
Design
I start by sketching and creating wax patterns by hand forming, mold reproduction or gathering organic elements such as lime slices.
Spruing
A sprue is added to my wax or organic piece strategically in a canister.
Investing
The wax tree is then put into an investment plaster cast which gets debubbled then hardens and sets.
Burnout
Canister goes into the kilm for approximately 5 hours. The wax is burnt out, leaving a cavity in the cast (this is why it is called lost wax casting because the wax is lost in the process).
Casting
Metal (silver, bronze, etc.) is liquified using a blow torch and is shot into the canister and fills up the mold using a centrifical force machine.
Clean up
This is where the stage of grinding, cleaning, and polishing happen. Then patina’s are applied, stones are set and treasures sparkle and shine.